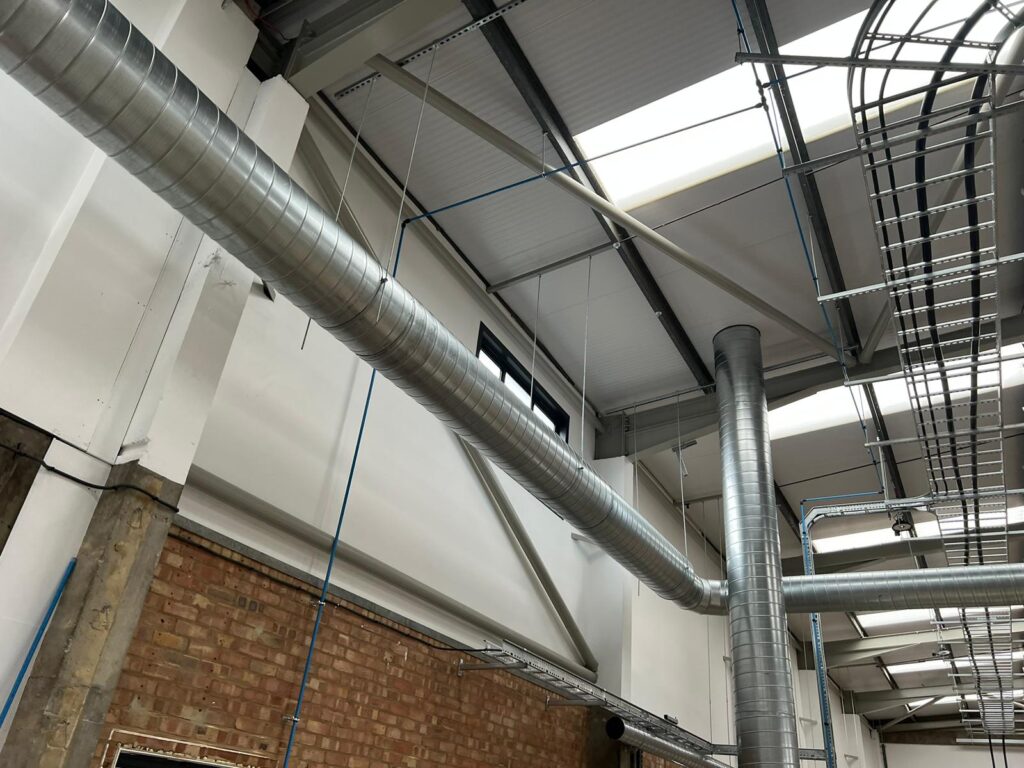
Enhanced Efficiency and Reliability through Compressors and Pipework Installation
Client Overview:
Industry: Fine Art Printing
Location: London, UK
Background: The client specialises in producing high-quality fine art prints, catering to artists, galleries, and collectors worldwide. With a new factory move and commitment to excellence and innovation, the client recognised the need to upgrade its compressed air system and pipework infrastructure to support its expanding operations efficiently.
Challenges:
- Outsized Equipment: The existing compressed air system consisted of an undersized compressor, resulting in inefficiencies and unreliable performance.
- Inadequate Distribution: Inefficient distribution of compressed air to printing machines and air tools due to outsized hoses, leading to pressure drops and operational issues.
- Expansion Requirements: The need to accommodate the growing production demands and ensure scalability of the compressed air system for future expansion.
Solution: In response to the challenges faced, the client decided to invest in a comprehensive upgrade of its compressed air system, including the installation of 2 new 4kw MARK screw compressors and a 20mm AirNet aluminium pipework ring main.
Implementation:
- Assessment and Planning: We conducted a thorough assessment of the client’s production requirements and existing infrastructure. Based on the assessment, a customised solution was designed to meet the company’s specific needs.
- Screw Compressor Installation: The outdated compressors were replaced with state-of-the-art screw compressors, chosen for their energy efficiency, reliability, and superior performance. The new compressors were installed to ensure optimal operation and seamless integration with existing systems.
- AirNet Pipework Installation: A 20mm AirNet aluminium pipework system was installed to optimise the distribution of compressed air throughout the facility. The AirNet pipework, known for its durability, corrosion resistance, and smooth interior surface, ensured efficient and reliable delivery of compressed air to printing machines and air tools.
- Testing and Optimization: Following installation, rigorous testing and optimisation procedures were conducted to ensure the entire compressed air system operated at peak performance levels. The client’s staff received comprehensive training on system operation and maintenance protocols.
- Scalability and Futureproofing: The upgraded compressed air system was designed with scalability in mind, capable of accommodating future expansion and increasing production demands.
Results:
- Improved Efficiency: The installation of new screw compressors and AirNet aluminium pipework significantly improved the efficiency of the client’s compressed air system. Reduced energy consumption and minimized pressure drops contributed to enhanced operational efficiency and productivity.
- Reliability and Performance: The upgraded system provided reliable and consistent compressed air supply, minimizing production downtime, and ensuring uninterrupted workflow in the fine art printing process.
- Enhanced Safety: The AirNet aluminium pipework system enhanced safety by minimizing the risk of leaks and pressure fluctuations, creating a safer working environment for employees.
- Cost Savings: The energy-efficient screw compressors and optimized distribution system resulted in cost savings for the client over the long term, reducing operational expenses and enhancing overall profitability.
Conclusion: The successful implementation of the MARK screw compressors and pipework upgrade exemplifies the client’s commitment to efficiency, reliability, and innovation in the fine art printing industry. By investing in modern technology and optimizing its compressed air system, the client has positioned itself for sustained growth and success in meeting the evolving needs of its clients and the market.